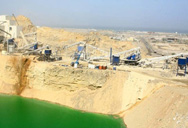
Analysis of material flow and consumption in cement
The material flow route for a cement plant was obtained. • Three mass balances for three cement production stages were established. • Each ton of products requires 2.48, 4.69, and 3.41 t of materials in three stages. • Waste gas recycling rate in
More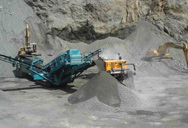
(PDF) Analysis of material flow and consumption in
The results show that approximately 2.48t, 4.69t, and 3.41t of materials are required to produce a ton of the product in raw material preparation, clinker production,
More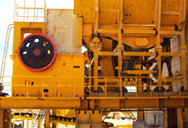
Failure analysis of a ball mill located in a cement’s production line
The work herein presented analyses an existing failure in a ball mill of a cement production line. • The failure is recurrent and responsible for reducing the period
More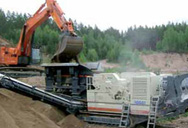
Analysis of material flow and consumption in cement
The results show that approximately 2.48 t, 4.69 t, and 3.41 t of materials are required to produce a ton of the product in raw material preparation, clinker
More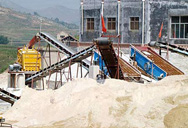
Ball Mill In Cement Plant - Cement Ball Mill AGICO Cement
Ball mill is the cement crushing equipment in the cement plant. Compared with open- circuit ball mill, the closed-circuit ball mill has high efficiency, high output, low cement
More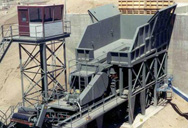
Cement Manufacturing Process Flow Chart
1. Convert the following flow chart into a paragraph of about 150 words. The process of making cement is described in this flow chart. The two raw materials used in
More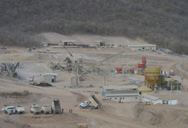
Flow Of Material In Ball Mill In Cement Plant
Cement ball mill is a kind of important cement equipment in the process of raw material preparation and finished product grinding in cement plants. it is mainly used to grind
More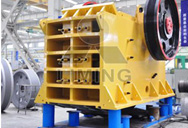
Heat Mass Balance in Cement Plant - SlideShare
Step2 Take 20-30 sets of reading of each cooler fan by vane anemometer and put the constant value in equation 2 such a way it matches with anemometer flow
More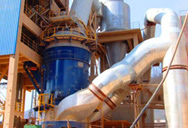
Flow Of Material In Ball Broyeur À In Cement Plant
broyeur components of a cement plant. Flow Of Material In Ball Broyeur In Cement Plant. 2021-12-18 A cement plant in matozinhos, brazil is one of brazils leading cement
More
Broyeur De Ciment - Dal Teknik
Broyeurs de type UDCM sont conçus pour atteindre une efficacité maximale de broyage, faible consommation d’énergie, la mise en page de plante compacte et la conception
More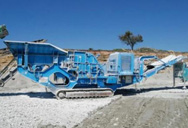
Cement mill - Wikipedia
A Ball mill is a horizontal cylinder partly filled with steel balls (or occasionally other shapes) that rotates on its axis, imparting a tumbling and cascading action to the balls. Material fed through the mill is crushed by impact and
More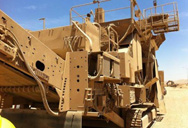
1 Cement Mill PDF Mill (Grinding) Cement - Scribd
Cement mill (Ball Mill) consists mainly of : - A rotation steel cylindrical shell supported at both ends on turning /. slide shoe bearings. - Liners for protecting the inside surface of the shell. - Diaphragms for dividing the mill into two or more compartments. - Grinding Balls. - Mill cooling system.
More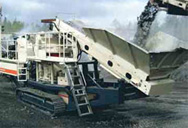
Ventilation Prediction for an Industrial Cement Raw Ball Mill by
rate, the data were collected from one of the Raw Material ball mill circuits (line 1) of the Ilam cement plant (Figure 1). This plant has 2 lines for cement production (5300 t/d). The ball mill has one component, 5.20 m diameter, and 11.20 m length with 240 t/h capacity (made by PSP Company from ì , Czechia).
More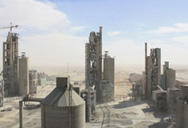
Volume 3, Issue 5, November 2013 Study of Processing and ... - IJEIT
stacking, raw material handling grinding, coal grinding, preheaterkiln cooler, clinker grinding (cement mill), packing plant loading plant, quality control. I. Cement users should wear protective clothing.INTRODUCTION Cement: In the most general sense of the word, cement is a binder, a substance that sets and hardens independently, and
More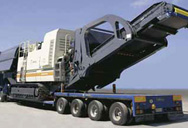
Ball Mill - an overview ScienceDirect Topics
Quantum Nanostructures (QDs): An Overview. D. Sumanth Kumar, ... H.M. Mahesh, in Synthesis of Inorganic Nanomaterials, 2018 3.6.1.1 Ball Milling. A ball mill is a type of grinder used to grind and blend bulk material into QDs/nanosize using different sized balls. The working principle is simple; impact and attrition size reduction take place as the ball
More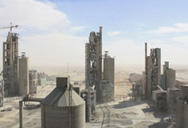
Dust Emission Monitoring in Cement Plant Mills: A Case Study in
The phenomenon was precisely the opposite of the level of 2019. However, we can note that the months of 2019 with a slightly higher level of dust concentration in the stack of the cement mill were August, with 4.6 mg/Nm 3, October, with 5.06 mg/Nm 3, and November, with 4.54 mg/Nm 3.
More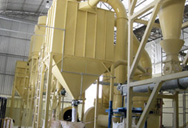
Comparing ball mills and VRMS for cement grinding
The equipment costs are higher for a VRM than a ball mill, reflecting the greater complexity of the system, which includes items such as the rollers, table and the hydraulic system. Overall, when equipment, erection and civil costs are taken into account, the cost of a VRM project is around 20 – 25% greater than a ball mill system of the same ...
More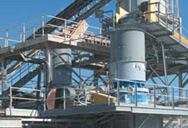
(PDF) La fabrication du ciment Souidi Ali - Academia
C’est au milieu du 19ème siècle que la structure du ciment fut vraiment découverte par le français Louis Vicat. Le ciment est produit en portant à une température de 1450 °C un mélange de calcaire et d’argile. On obtient alors des nodules durs appelés clinker.
More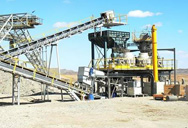
Digitization and the future of the cement plant McKinsey
There’s never been a more important time to build resilience into the core of the cement value chain: the cement plant. The cement industry is being hit hard by the COVID-19 pandemic, with global demand for cement expected to decline by 7 to 8 percent in 2020—though these declines have been unevenly distributed across regions. 1 Paul
More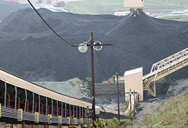
Cement - Wikipedia
Cement is seldom used on its own, but rather to bind sand and gravel ( aggregate) together. Cement mixed with fine aggregate produces mortar for masonry, or with sand and gravel, produces concrete. Concrete is the most widely used material in existence and is behind only water as the planet's most-consumed resource.
More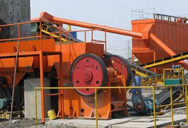
A Review on Pyroprocessing Techniques for
The energy efficiency of dry ball-mill grinding of cement depends on factors such as ball charge fill-ratio, mill length/diameter ratio, size distribution of the ball charge, operating conditions of the air
More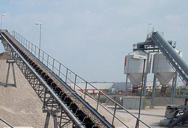
DESIGN AND ANALYSIS OF BALL MILL INLET CHUTE FOR ROLLER PRESS
Ball mills (Fig 1.1) are coming in cement plant areas of raw grinding, coal grinding and cement grinding which in turn as raw mill, coal mill and cement mill. Ball mills are horizontal tube mills having single or two compartments for grinding, Balls as grinding media and driven by side or central drive.
More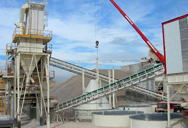
Ball Mill In Cement Plant - Cement Ball Mill AGICO
Of course, even if we set a more appropriate cement fineness, it is difficult to change the current situation that the flow velocity in the open-circuit ball mill is only 1/2-1/3 of that in the closed-circuit ball mill with the same
More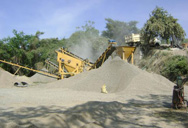
(PDF) Environmental Pollution by Cement Industry
The level of pollution generated by the cement industry is such that, to obtain one ton of cement, the equivalent of 0.8-1 tons of CO 2 is emitted into the atmosphere, contributing greatly to ...
More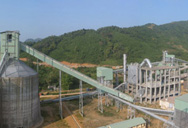
Mass balance of the cement mill system. Download Table
Context in source publication. ... the cement plant, 3.41 kg of materials is required to produce a kg of cement in the final stage. Ambient air (2.40 kg/kg cement) and clinker (0.84 kg/kg cement ...
More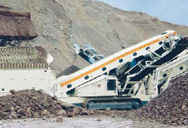
Cements ground in the vertical roller mill fulfil the quality ...
In the study, raw materials including clinker, gypsum, pozzolan were separately milled on a ball mill (the ball mill size: φ500 mm × L500 mm, productivity: 5 kg / grinding time) to achieve the ...
More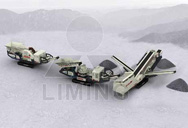
Ventilation Prediction for an Industrial Cement Raw Ball Mill by
the data were collected from one of the Raw Material ball mill circuits (line 1) of the Ilam cement plant (Figure1). This plant has 2 lines for cement production (5300 t/d). The ball mill has one component, 5.20 m diameter, and 11.20 m length with 240 t/h capacity (made by PSP Company from Prerˇ ov, Czechia).
More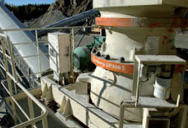
Raw Material Drying-Grinding - Cement Plant Optimization
Drying of moisture in raw materials is required for effective grinding and subsequent handling of raw meal. This is achieved normally by ducting part of the kiln exhaust gas through the mill with inlet temperatures of up to 320°C. However, when starting from cold, when hot gases are not available from kiln, Hot gas is provided by Oil fired Hot ...
More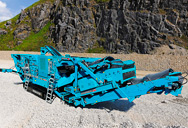
Energy-Efficient Technologies in Cement Grinding IntechOpen
The energy consumption of the total grinding plant can be reduced by 20–30 % for cement clinker and 30–40 % for other raw materials. The overall grinding circuit efficiency and stability are improved. The maintenance cost of the ball mill is reduced as the lifetime of grinding media and partition grates is extended. 2.5.
More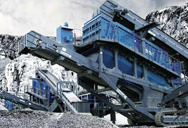
(PDF) Parametric Studies of Cement Production Processes
Cement production processes involve complex chemical and physical reactions during the conversion of raw materials to the final product. Moreover, the clinker burning process, which has a decisive ...
More