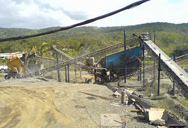
Grinding Mill - an overview ScienceDirect Topics
The principle objective for controlling grinding mill operation is to produce a product having an acceptable and constant size distribution at optimum cost. To achieve this objective an attempt is made to stabilize the operation by principally controlling the process variables.
More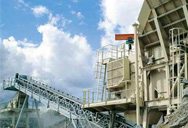
Coal Mill - an overview ScienceDirect Topics
1. To control the quality of coal being sent to the burners located on the furnace walls. The word quality here means the temperature and fineness of the PF. The set temperature
More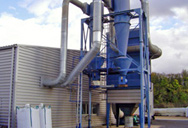
Mining Industry: What is a coal mill? - Quora
VDOM DHTML tml>. Mining Industry: What is a coal mill? - Quora. Something went wrong.
More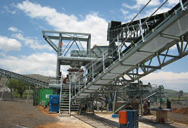
Coal Grinding - Cement Plant Optimization
Most commonly used mills for coal grinding in cement plants are closed circuit air swept (Single chamber) ball mills and vertical mills. Ball Mill: Single chamber ball mills (with
More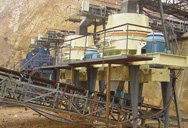
Vertical Grinding Mill (Coal Pulverizer) Explained
Introduction. This article concerns itself with vertical grinding mills used for coal pulverization only (coal pulverizers), although vertical grinding mills can -and are- used for other purposes.. The 3D model in the saVRee
More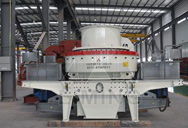
Coal Mill In Cement Plant, Air-swept Coal Mill Coal Mill
Air-swept coal mill is the main equipment of cement plant, also called coal mill in cement plant, used for grinding and drying various hardness of coal, crushing the coal briquette into pulverized coal.It is the important auxiliary equipment of pulverized coal furnace. The air-swept coal mill runs reliably, can work continuously, also has a large production
More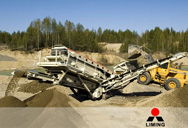
Mill (grinding) - Wikipedia
A mill is a device, often a structure, machine or kitchen appliance, that breaks solid materials into smaller pieces by grinding, crushing, or cutting. Such comminution is an important unit operation in many
More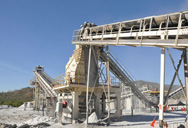
DISCUSSION ON SAFETY PRODUCTION OF COAL MILLING
1 Potential safety hazards in the coal mill system. 1.1 Spontaneous combustion occurs. The process of cement production determines the need to use a large amount of coal. The use of coal is mostly ...
More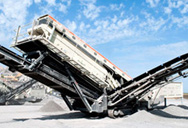
The coal grinding
Following the coal grinding world practice, Energosteel company specialists among the first offered for customers to use grinding balls the 4-th and 5-th hardness groups for coal grinding. Numerous tests have proven that use of grinding balls with a 4th and 5th hardness groups leads to a significant reduction a prime cost of
More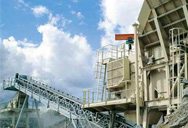
Coal Mill in Cement Plant Vertical Roller Mill Air-Swept Ball Mill
It is a mechanical device used to grind raw coal into pulverized coal powders. The most used coal mills in cement plants are air-swept ball mills and vertical roller mills. At present, most cement plants use coal as the main fuel in the clinker production process. The standard coal consumed by the new dry process for producing 1 ton of cement ...
More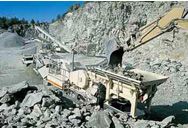
Coal Mill - an overview ScienceDirect Topics
Observer-Based and Regression Model-Based Detection of Emerging Faults in Coal Mills. Peter Fogh Odgaard, ... Sten Bay Jørgensen, in Fault Detection, Supervision and Safety of Technical Processes 2006, 2007. 5.2 Experiments with and design of the regression model-based approach. Operating data from a coal mill is used to compare the fault detection
More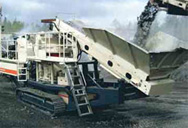
Final Report On Mill Modelling PDF Mill (Grinding) Coal
(a) Tarong coal Fig. 1.2 (a): E-mill model simulation output for two coal samples in Excel spreadsheet interface Protocols for Best Practice in Coal Grinding in Power Stations 8 Julius Kruttschnitt Mineral Research Centre (JKMRC) and China University of Mining and Technology (CUMT) (b) Yulin coal Fig. 1.2 (b): E-mill model simulation output for two
More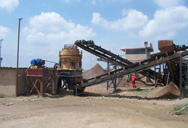
Grinding Mill - an overview ScienceDirect Topics
In SAG mill operation, the grinding rate passes through a minimum at a “critical size” ( Chapter 5 ), which represents material too large to be broken by the steel grinding media, but has a low self-breakage rate. If the critical size material, typically 25–50 mm, is accumulated the mill energy efficiency will deteriorate, and the mill ...
More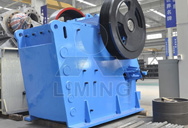
Vertical Coal Mill for Coal Grinding in Cement Plant Power Plant
Vertical Coal Mill. Feeding size: ≤110mm. Capacity: 5-70t/h. Motor power: 110-1400kW. Applications: Vertical coal mill is mainly used for grinding raw coal, bituminous coal, and other fuels into coal powder, which is supplied to rotary kiln and other kilns in the cement plant and thermal power plant. Email: info@ballmillssupplier.
More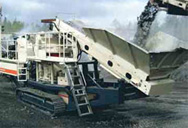
Boiler Mill and Coal Pulverizer Performance GE Steam
YES. Our boiler mills and coal pulverizers span the globe and are built in a variety of sizes and capacities. We provide customized maintenance solutions, and offer a full spectrum of high-quality solutions for each—in
More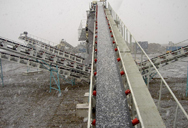
(PDF) 43 Drying of Coal - ResearchGate
43.2.8 Mill-Type Dryers ... quality of grinding (if coal is ground), and impedes. separation and classification as well as the pneumatic. transport of pulverized coal. Friable coal suitable for.
More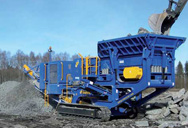
Mill Training Manual Alstom PDF Coal Mill (Grinding) - Scribd
Coal is volume of hot air or a longer residence time for the coal in the. subjected to a grinding force between a rotating bowl and three mill is required to properly dry and grind the coal. Hence, mill. grinding rolls. Since there is no metal-to-metal contact capacity (pounds per hour) is reduced.
More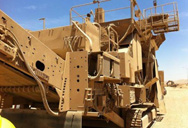
(PDF) Improving the efficiency of the coal grinding process in ball ...
Curves of mill productivity, power consumed, specific surface of coal dust in terms of the relative rotational speed of the ball drum mill Composition of the balls loading the mill with a standard ...
More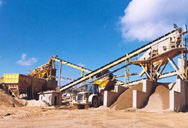
Grinding mills: how to accurately predict their power draw
High Pressure Grinding Rolls (HPGR) circuits have the potential to reduce these emissions by up to 32.8 Megatonnes/year, or 44.3% when compared to the Semi-autogenous/ball mill circuit alternatives.
More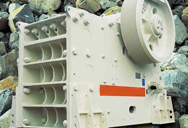
Optimization of operating conditions on ultra-fine coal grinding ...
This study investigated ultra-fine coal grinding performance of four low- to moderate-cost grinding media in a laboratory stirred mill. Kinetic grinding tests showed that silica beads generated the finest product size with a P 80 of 5.9 μm from a feed size of 24.4 μm while having a specific energy (SE) input of 309 kWh/ton. Nonetheless, the least
More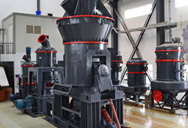
Determining Optimum Productivity of a Ball Drum Mill When
Abstract Ball drum mills (BDM) are one of the main types of coal-grinding equipment in Russia. A significant drawback of BDM is high power consumption (a significant part of the TPP’s own needs). With a huge scale of production, reducing these costs even by a few percent gives a significant economic effect. The problem of
More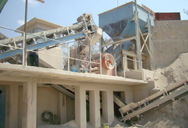
The Effects of Moisture Content and Coal Mixtures on the Grinding
In this article, effects of moisture content and coal mixtures on grinding properties of the samples of two different fine coals, which were used in the Göltaş Cement Factory in Isparta (Turkey ...
More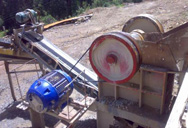
Comparison of energy efficiency between ball mills and
It is a 30-40% more energy-efficient advanced grinding mill than the ball mill, especially for grinding below 100 lm [32][33][34][35] [36]. The breakage mechanism in stirred mills differs from ...
More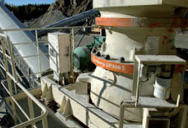
Raw Material Drying-Grinding - Cement Plant Optimization
Drying of moisture in raw materials is required for effective grinding and subsequent handling of raw meal. This is achieved normally by ducting part of the kiln exhaust gas through the mill with inlet temperatures of up to 320°C. However, when starting from cold, when hot gases are not available from kiln, Hot gas is provided by Oil fired Hot ...
More