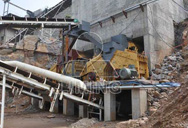
Ball mill - Wikipedia
A ball mill, a type of grinder, is a cylindrical device used in grinding (or mixing) materials like ores, chemicals, ceramic raw materials and paints. Ball mills rotate around a horizontal axis, partially filled with the material to be ground plus the grinding medium. Different materials are used as media, including ceramic balls, flint pebbles, and stainless steel balls. An internal cascading effect reduces the
More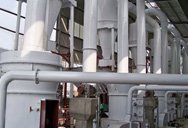
Ball Mill - an overview ScienceDirect Topics
The ball mill is a tumbling mill that uses steel balls as the grinding media. The length of the cylindrical shell is usually 1–1.5 times the shell diameter ( Figure 8.11 ). The feed
More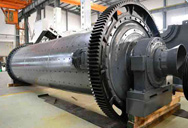
Grinding Media - Union Process
Composition. metallic grinding media like carbon steel, forged steel, stainless steel or chrome steel grinding balls are best for some applications, while others require non-metallic media made of
More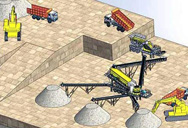
Grinding Balls Rods - 911 Metallurgist
The original charge to a mill is generally between 40% and 50% of mill volume for ball mills and 35% to 45% mill volume for
More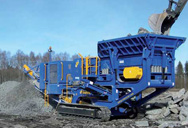
Precision Balls - RGPBALLS
Choosing means Quality In-house metallographic and metrological laboratory for analyses of the microstructures of steel. Speed 6,000 square-metre warehouse in a single location
More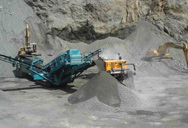
Ball Mill Balls factory, Buy good quality Ball Mill Balls products
Dia 20mm-150mm Grinding Media Forged Steel Ball Cast Iron Ball for Ball Mill Brief Description: Forged Balls Size: 20-150mm Inspection: SGS/BV/TUV Origin: Shandong,
More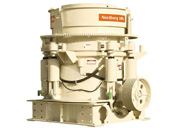
Mill (grinding) - Wikipedia
Ball mills normally operate with an approximate ball charge of 30%. Ball mills are characterized by their smaller (comparatively) diameter and longer length, and often have a length 1.5 to 2.5 times the diameter. The feed is
More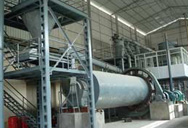
Ball Mill Balls - Manufacturing Of High Quality Ball Mill
Ball mill balls are a type of ball used in ball mills, usually made of high-hardness materials such as steel, ceramics, hard alloys, etc. Ball mill steel balls is an important part of the ball mill, its main function is to carry
More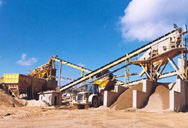
Method for manufacturing high-chrome cast iron grinding balls
By analyzing metallographic structure and performance variations of high-chrome alloy balls through composition design and experiment researches of the high-chrome alloy
More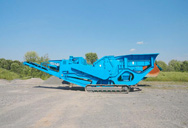
Grinding Media - Union Process
Composition. metallic grinding media like carbon steel, forged steel, ... Silicon Carbide Balls are very high-cost grinding media that are used for milling same materials (silicon carbide ball to mill silicon carbide
More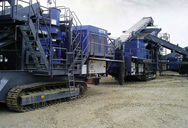
Ball charges calculators
-Modification of the Ball Charge: This calculator analyses the granulometry of the material inside the mill and proposes a modification of the ball charge in order to improve the mill efficiency: - Ball charges composition: These calculators give the gradation of the ball charge in function of predefined conditions:
More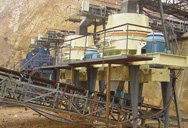
Ball Mill Balls - Manufacturing Of High Quality Ball
Ball mill steel balls is an important part of the ball mill, its main function is to carry out the grinding operation in the ball mill, and the material is crushed into the required size. Ball mill balls usually have the
More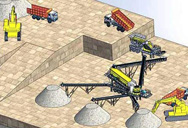
Grinding Balls Rods - 911 Metallurgist
Grinding Balls. Steel balls ranging from ¾ to 5 in. in diameter are used. Rods range from 1½ to 4 in. in diameter and should be 3 to 4 in. shorter than the inside mill length. Tube mills are usually fed balls smaller than 2 in., whereas 4- or 5-in. balls are more commonly used for ball-mill grinding.
More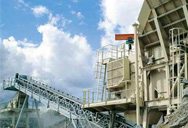
Optimum choice of the make-up ball sizes for maximum
(23) gives the optimum composition of 40% 50.8 mm ball and 60% 25.4 mm balls for a 1 m diameter mill, and 27% 50.8 mm and 73% 25.4 mm for a 2 m diameter mill when grinding from a 90% passing 9.5 mm feed to an 80% passing 150 μm product.
More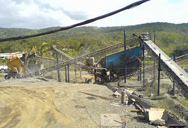
Ball Mills - 911 Metallurgist
CERAMIC LINED BALL MILL. Ball Mills can be supplied with either ceramic or rubber linings for wet or dry grinding, for continuous or batch type operation, in sizes from 15″ x 21″ to 8′ x 12′. High density ceramic linings of uniform hardness male possible thinner linings and greater and more effective grinding volume.
More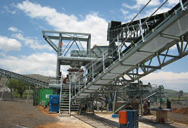
Manufacture process of rolling ball, forging ball and casting balls ...
The casting grinding ball is a kind of grinding balls which uses the medium frequency electric furnace to melt the scrap steel, scrap iron and so on. The furnace charge is fully melted and the precious metal alloy (such as ferrochromium, Ferromanganese, ferrovanadium, etc.) is added to the furnace for chemical composition conditioning.
More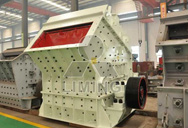
Ball Mill Grinding Characteristics with Respect to the Chemical ...
Ball mill grinding tests were conducted using four domestic pyrophyllite samples with similar chemical compositions but different utilisation. Based on the kinetic grinding model, the breakage constants were determined experimentally and by a personal-computer-based inversion method.
More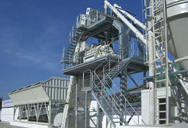
Grinding Ball Wear Breakage by Impact Abrasion Tests
Small-scale ball mill tests are convenient but could give misleading results because they do not produce the severe ball impacts of full-sized mills. During ball milling, balls ... The flaws in the cast balls included surface roughness from sand casting and presence of a parting line, Fig. 1b. The compositions of the steel balls, ...
More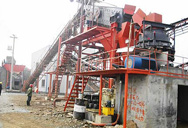
邦德球磨功指数试验的影响因素*-Influencing Factors of Bond ...
Abstract:Bond ball mill work index is an important tool for the comminution flow-sheet design of mineral processing plant and the efficiency evaluation of comminution circuit performance.The difference of ball composition and mill body structure in different commercial Bond ball mill work index tests has always been ignored.
More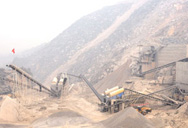
Comparison of grinding media—Cylpebs versus balls
As a result, for a given charge volume, about 25% more grinding media surface area is available for size reduction when charged with Cylpebs, but the mill would also draw more power. Table 1. Comparative data of physical properties for Cylpebs and balls. Cylpebs ( γ = 7.65 kg/l) Balls ( γ = 7.85 kg/l)
More
Everything you need to know about clinker/cement
ball charge composition will allow an even better mill operation. Ball Charge Wear Rates. Net wear rate = process wear rate (loss of tonnage inside the mill during grinding) Gross wear rate = purchasing wear rate
More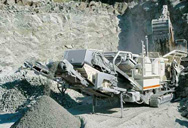
(Received: February 1, 2016; Accepted: November 4, 2016)
Secondary ball mill balls experience significant levels of abrasive and corrosive wear, with insignificant levels of impact wear due to the small 2.5 – 60 mm diameters. They experience 25 – 40% less wear than in primary grinding of the same ore. High chromium balls may be economical for high
More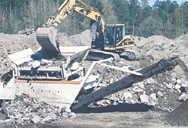
GM Balls – Atul Engineering
Heat treatment: The grinding media is heat treated to obtain the required hardness and microstructure. Balls diameter (mm) – 125, 100, 90, 80, 75, 70, 65, 60, 50, 40, 30, 25, 20, 17, 15. Cylpebs (mm) – 35 x 35, 25×25, 22×22, 19×19. Hardness: When tested in accordance with IS 1500/1983 the hardness at any point across the section of the ...
More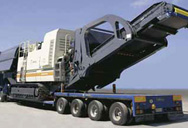
mill ball composition first quantum minerals ltd
First Quantum Minerals Ltd. ("First Quantum" or the "Company") (TSX:FM) being the SAG mill and the ball mill, have been ordered and engineering design has commenced.
More
Ball Mill, Construction, Working Principle, Application,
Ball mills produce 1 to 50 ton/h power of which near about 70 to 90 percent would pass a 200 mesh screen and the energy requirement of a ball mill is about 16 kWh/t. In the case of the batch-operated mill, a measured quality of a solid to be ground is charged into the mill through an opening in the shell.
More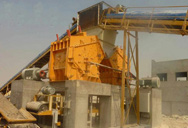
Casting chrome grinding media balls - crusher balls-mill ball-steel ball
Casting Grinding media balls, so called as crusher balls, mill balls, steel balls, is widely used in cement. mining and power station.
More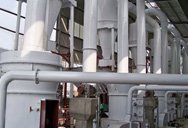
Heat treatment process for high chromium grinding ball
The heat treatment process is the use of two-stage heat quenching and low-temperature tempering. At the rate of less than 70 °C / h, the temperature is increased to 650-680 °C for 2 hours, at the temperature increasing to 950 °C for 4 hours, forced air-cooling, oil-cooling, and special quenching liquid cooling respectively, and tempering is ...
More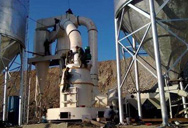
Ball Mill (Ball Mills Explained) - saVRee - saVRee
For both wet and dry ball mills, the ball mill is charged to approximately 33% with balls (range 30-45%). Pulp (crushed ore and water) fills another 15% of the drum’s volume so that the total volume of the drum is 50% charged. Pulp is usually 75% solid (crushed ore) and 25% water; pulp is also known as ‘ slurry ’.
More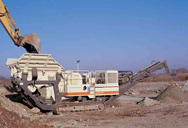
No. Name of the item Specification CHEMICAL METALLUGICAL
the date of declaring the mill as test mill”. 2. HI-CHROME LINERS FOR BALL TUBE MILLS BBD-4772 and BBD - 4760 HI-CHROME LINERS for Ball Tube Mills BBD-4772 and BBD-4760 having following specifications:- A) Technical Specfications 1. Chemical Composition: C: 2.4 to 2.8% Ni: 0.2 to 0.5 % Cr: 22.0 to 28.0% Mo: 0.2 to 0.6 %
More